Do you have a lawnmower deck that has small holes starting to form? Ever consider taking up hobby welding to make your own mower deck welding repairs. Hobby welding is more than just learning to make artistic creations.
Once you learn the basics of welding you’ll be able to make repairs to all kinds of home products and equipment too. The repairs you’ll be able to take on are endless.
If you’ve read any of our other articles on hobby welding, you’ll know that I’m not a professional welder. Guess what, you don’t need to be a professional to be successful at making your own projects and repairs. All you need is the desire to learn and a little practice.
If you want more information on what it takes to get into welding, our article on How To Get Started Welding has some good information.
This article is about how I’ve been able to repair several small holes on our aging lawnmower deck. By repairing the holes when they were small, it prevented them from getting larger and jeopardizing the overall integrity of the mower deck.
How Do Holes Form In Mower Decks
Table of Contents
From my experience, I believe there are two different ways holes typically form. The first is from rusting and the second is from abrasive wear. Obviously, how much use your mower gets is going to play a significant role too. But there are things you can do to help prevent holes from forming.
To help prevent rusting I recommend thoroughly cleaning the underside of the mower and coating it once a year. As you’re probably aware, there are areas under the mower deck that wet grass sticks and cakes on. The area under this moist grass is a prime spot for rust to begin. By cleaning, priming, and painting the underside of the mower once a year makes a huge difference.
The abrasive wear is more difficult to prevent. The cleaning and painting will help, but the underside of a mower deck is a very harsh environment. Whirling and flying sand and grit takes its toll over time. Even if rusting doesn’t cause holes, eventually wear will get you.
When To Repair Holes In Your Mower Deck
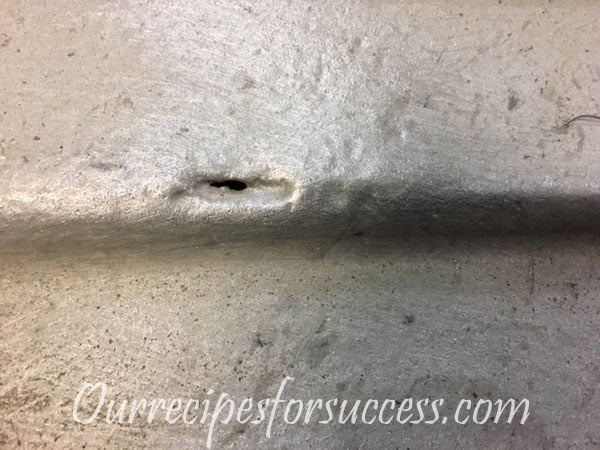
My mower is over 30 years old and is still going strong. But after about 20-25 years I started finding the occasional hole beginning to form. This is when you need to make the repairs; when you first notice them. Many of these areas are susceptible just by where they are located on the mower. By repairing these areas quickly you reinforce them and protect the area from further “erosion”.
If left alone, the holes will only get bigger and the surrounding area can become even thinner making the repair a little more difficult. When this happens, you have to weld a patch over the entire area.
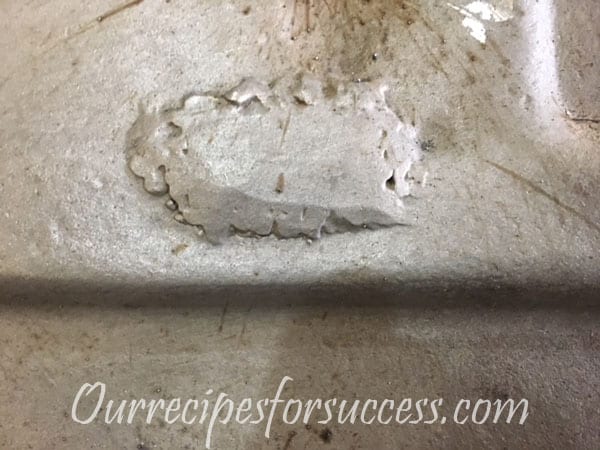
If holes are not repaired and become larger, there are other potential negative effects. Mowing debris could fly up through the holes possibly hitting the rider or at least hit the underside of the garden tractor causing damage.
The other potential issue is if the hole is near a mower blade spindle or a mower deck lifting bracket. This could affect the overall integrity of the mower deck, which could lead to cracking or a catastrophic failure. Making repairs to small holes is always the best solution.
Preparing To Make The Welding Repair
Before you can make the repair the area around the hole will need to be cleaned. A wire brush works well for this. Sanding disks clean okay, but they may be too abrasive, especially when you’re dealing with thin metal. I recommend sticking with a wire brush and getting the area as clean as possible.
To make repairs on thin metal like this your best bet is to use a MIG, or wire welder, versus a stick, or arc welder. There are other options, such as a TIG welder, but for most hobby welders a “flux core welder” is a great entry-level welder.
It’s basically the same as a MIG welder, except without the gas. It’s what I use and does a good job. You will want to start out with the welder set at the lowest amperage setting, because of welding on thin metal.
How To Make The Welding Repair
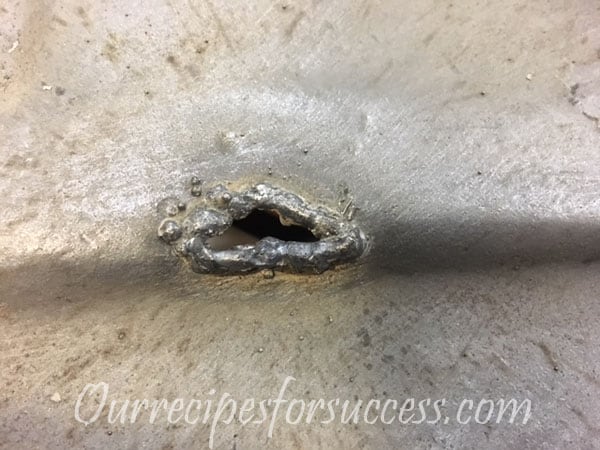
The best way to weld small holes in thin metal is to begin by putting a small weld bead around the perimeter of the hole. Nine times out of ten as soon as you start welding on the thin metal it will burn through making the hole large. Don’t panic, that’s to be expected. That’s why we want to start when they’re small.
To combat this it helps to keep the amperage (heat) setting as low as possible. Welding in short bursts of one second helps too. It allows the red hot metal time to cool before striking your next arc.
You can also alternate welding on the opposite side of the hole and continue going back and forth with the one-second arcs until you have established the perimeter bead around the hole.
Once you have the first perimeter bead made I like to run a wire brush over the weld again. This is to clean up any loose debris that may be present. If you’re a beginner and are using flux core wire, there may be some flux residue. Regardless, there could be some burnt organic material or paint and primer left behind. It’s always best to give it a quick brushing before continuing.
To complete the repair just repeat the above steps. Just add to the weld bead you made on the previous pass and clean it before making the next pass. Once the hole is filled you’re basically done.
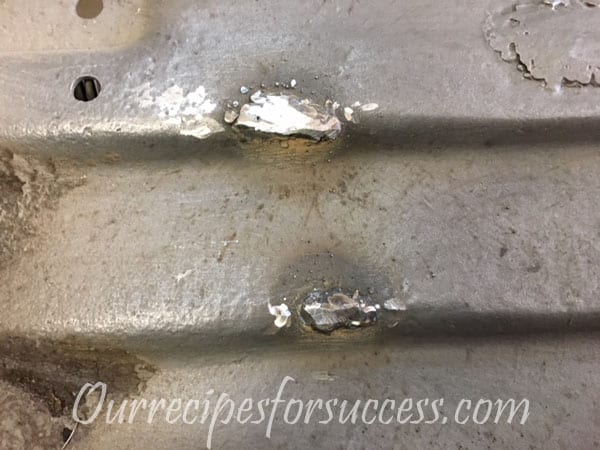
It doesn’t have to be beautiful! In fact, welding on old, thin, dirty metal is actually more difficult. The fact that you are able to fill it is awesome! You can always smooth it out some with a grinder if it makes you feel better. I’ve been there, done that. Then once it’s cooled spray it with a little primer and paint, top and bottom, and you’re good to go.
Conclusion
Whether you want to call this “hobby welding” or “DIY welding”, there are many repairs a beginning welder can safely make. As mentioned earlier, I am not a professional welder. However, if you check out some of my other “welding repair projects” you will definitely see how beneficial being able to weld can be!
Being able to weld has saved me many hours, if not days, in running to welding repair shops, waiting for repairs, and spending hundreds of dollars. I’m confident hobby welding can work for you too. Get started today.
If you have any comments or questions, you can leave them in the comments section below or you can email us at [email protected]. FYI, we do not collect or share email addresses. We will only use them to reply to your comments or provide answers to your questions. We are also required to let you know that some of our links are “affiliate links”. This means if you click on a link and make a purchase, we could make a small commission, at no extra cost to you. This helps offset the cost of maintaining our website. So, if you like what you’ve seen, please be sure to give us a “Like” and “Share” on Facebook and Instagram too. Thank you for reading and good luck with all your home projects!
You’re welcomed!
Thank you for the inf